Feathering the propeller:
If there is an engine failure in flight, the propeller would windmill creating drag and increasing any damage that had occurred in the engine. Feathering is the procedure by which the propeller blades are turned beyond the coarse pitch position until they are edge on to the airflow. This action stops rotation and reduces the drag of the stationary propeller to a minimum.
As present we are only considering the single acting propeller mechanism which adopts the use of a spring to force the propellers to the feathered position. Students should be aware that on some hubs a nitrogen charge within the hub provides the force to feather. Double acting variable pitch propellers which will be looked at later use electrical feathering / auxiliary oil pump to provide the force for feathering.
Because of the dangers at overspeed all turboprops will have some form of Auto Feather which will be activated by a negative torque signal, these devices may give an electrical signal to energise a solenoid or hydro-mechanical as seen in Fig.
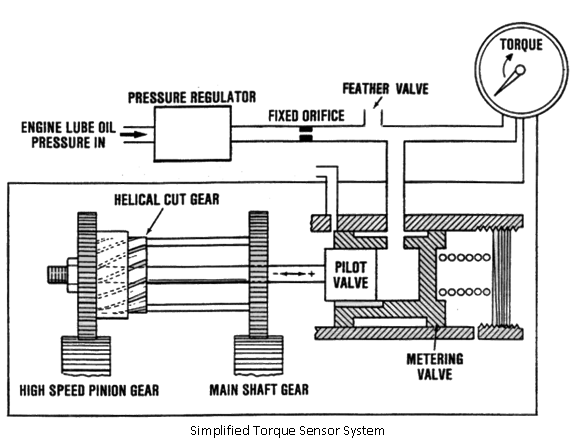
The torque sensor is a pressure regulator and regulates the 'torque' pressure as a result of the twisting action of the torsion shaft. The pressure in the reduction gearcase operates at less than ambient due to the action of the oil system scavenge pumps that pump oil and air out of the case. The torque sensor and metering valve sense this pressure. The torque sensor pilot valve is mechanically positioned and any change in case pressure will change the measured torque pressure. The gearcase pressure must be added to the torque sensor pressure. A pressure gage can measure the case pressure and this value added to the torque sensor pressure will give a corrected torque valve.
The propeller feathering valve is externally mounted on the rear of the reduction gearcase. The feathering valve is hydraulically actuated by the negative torque sensor and can be manually actuated by pilot control. The feather valve prevents high pressure control oil from entering the propeller dome and piston, which allows the spring-loaded propeller blades to move towards a feathered position.
Positive torque is when the engine is driving the propeller. If the engine should have an inflight shutdown, the windmilling propeller will drive the engine. This is considered to be negative torque. When the propeller is driving the engine, a torque sensor within the reduction gearcase senses a negative input. The negative torque system automatically effects a movement of the propeller blades toward the feather position. That propeller will not feather, however, it will continue to windmill. The negative torque system is automatic drag reduction and not an automatic feather system.
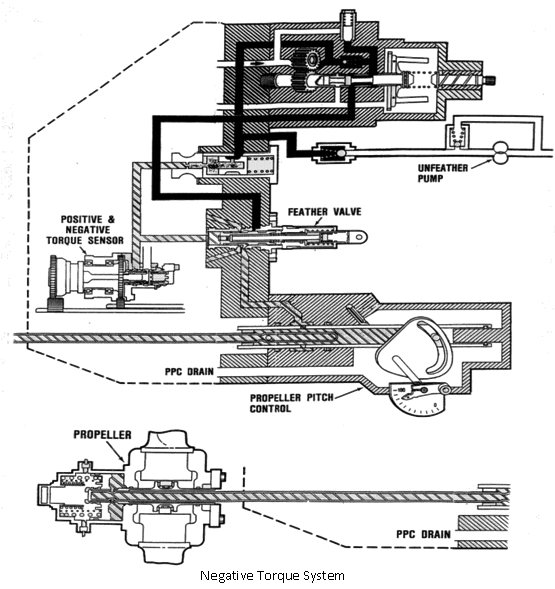