Implementation of Material Requirement Planning:
The total requirements for a material from an MRP schedule are given in the following table :
Week

The annual demand for this end item is estimated to be 25,000 units over a 50 week per year schedule, or an average of 500 units per week. It costs Rs. 800 to change over the machines in the ultimate assembly department to this end item when a production lot is begun. It costs Rs. 1.10 per unit when one unit of this product must be carried in inventory from one week to another; thus, when one unit of this product is in ending inventory, it should be carried over as beginning inventory in the next week and incurs the Rs. 1.10 per unit carrying cost. Find out which of these lots sizing methods results in the least carrying and changeover (or order) costs for the eight week schedule:
1. Lot for Lot (LFL),
2. Economic Order Quantity (EOQ), or
3. Period Order Quantity (POQ).
Solution
(a) Develop the total carrying costs over the eight week schedule for the lot-for-lot method. Lot-For-Lot (LFL) production lots equal the net requirement in each period.
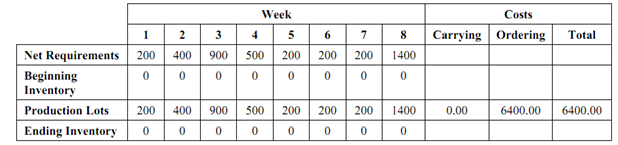
Ordering costs = Numbers of orders × 800.00 = 8 × 800.00 = 6400.00
(b) Develop the overall carrying costs over the eight week schedule for the EOQ lot sizing method. EOQ production lots equal the computed EOQ. First, compute the EOQ :
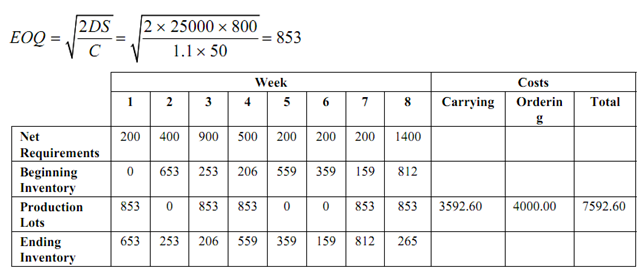
Carrying costs = total of ending inventories × 1.10 = 3266 × 1.10 = 3592.60
Ordering costs = Number of orders × 800.00 = 5 × 800.00 = 4000.00
(c) Develop the overall carrying costs over the eight week schedule for the POQ lot sizing method. POQ production lots equal the net requirements for POQ computed periods.
First, compute the POQ:
POQ = Number of weeks per year/ Number of order per year
= 50/(D/ EOQ) = 50/(25000/853)
= 1.706 or 2 weeks per order
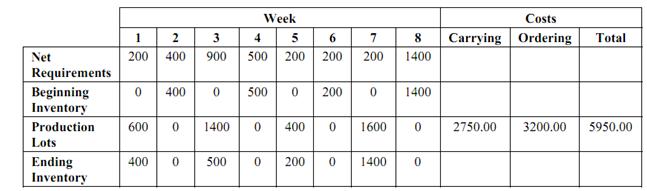
Carrying costs= sum of ending inventories × 1.10 = 2500 × 1.10 = 2750.00
Ordering costs = Number of orders × 800.00 = 4 × 800.00 = 3200.00
Among the lot sizing methods considered for this data, the POQ method exhibits the least carrying and ordering cost for the eight week net requirements schedule.
1. Where is MRP implemented?
2. Explain different lot sizing methods.