Supply Chain Quality Control
We are aware that the global manufacturing industry consists of a matrix of suppliers and customers linked with complex demands. Supply chain includes the suppliers who provide the raw material, the internal transformational process and the downstream distributions channels of distributors and retailers. For example, in a typical automobile manufacturing organisation, the chain covers in its ambit, tier II suppliers of raw materials and parts, tier I suppliers, the original manufacturers (OEMs), the sub assemblers, the wholesalers and the dealers. Quality control has a greater significance in the supply chain of the manufacturing industry where the number of players is large. The manufacturer has to ensure conformance to product quality specification by a collaborative quality control strategy with suppliers across the globe in real-time. The parameters of quality control should include the flow and transformation of goods from the raw materials to finished product and also cover the flow of information related to quality.
Quality control experts Donovan and Maresca suggest the following steps for successful supplier control:
- Create a cross- functional team.
- Determine critical performance metrics.
- Determine minimum standards of performance.
- Reduce the supplier base to those able to meet minimum performance requirements.
- Assess supplier performance:
- Supplier quality systems assessment.
- Supplier business management
- Supplier product fitness for use.
The detailed quality control activities focus on co operation during contract execution, supplier certification, supplier rating, and quality measurement for supplier relations.
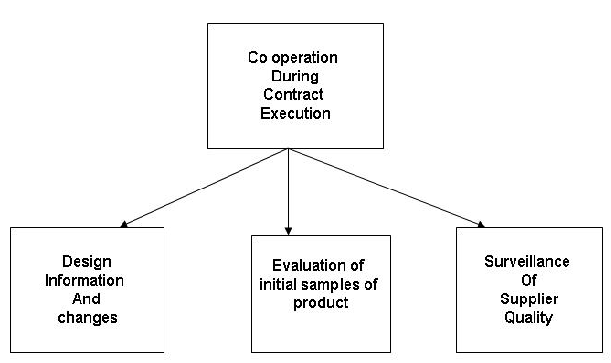
Figure : Cooperation during contract Execution
The figure describes the cooperation that concentrates on the activities that are described listed in detail.
Evaluation of initial samples of product: Under many situations, the supplier must submit test results of a small initial sample produced form production tooling and a sample from the first production shipment before the full shipment is done.
Design information and changes: Design changes might take place at the initiative of either the buyer or the supplier. Either way, the supplier should be treated like an in-house department when developing procedures for processing design changes.
Surveillance of supplier quality: The continuous monitoring and verification of the status of procedures, methods, conditions, processes, services and analysis of records in relation to stated references to make sure that specified requirements for quality are being met is termed as quality surveillance.
A useful tool for learning about a supplier's process and comparing several suppliers' manufacturing product to the same specification is termed as histogram. In case of a histogram, a normal sample is chosen forma lot and measurements are made on selected quality characteristics. The data are charted as frequency histograms. The analysis consists of comparing the histograms to the specification limits.
Communications to the supplier on non conformance must include a precise description of the symptoms of the defects.